UK: Fast-cooling furnaces
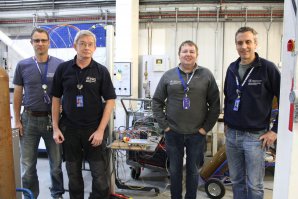
The ISIS furnace team
How long does it take to cool a sample environment furnaces from 1000˚C to 80 C? Answer: 4.5 hours. This wastes a lot of precious neutron beam time so what has SINE2020 been doing about it?
Many neutron experiments are performed in a vacuum and so sample environment equipment needs to be well-insulated – this causes a bit of a problem when you want to cool your sample back down. The laws of physics just get in the way! The last few hundred degrees are particularly difficult and slow. Currently the routine is to fill the furnace once it gets to 150°C with a gas, let the temperature cool and level, and then evacuate this hotter gas before refilling the vessel once more. The filling process is manual and the whole process is time-consuming.
Fortunately, Chris Goodway, Paul Mcintyre, Graham Burgess and Adam Sears at ISIS Neutron and Muon Source (picture right) have been working on this problem to make the process quicker and more efficient.
Their first step was to establish the maximum temperature the gas could be let into the furnace without over heating the outer tail. After a series of tests this was established at 500°C. The next stage was to set up a flow of cooling gas instead of using the batch process described above. This allows the gas to remove the heat as it flows through. The team tried several types of gases: helium, argon and nitrogen, at both room temperature and cooled through a liquid nitrogen cooling loop, but discovered that the traditional gas used, helium, was the best (this is reclaimed after the cooling process so it does not waste helium).
Next they investigated the best flow rate to use i.e. the rate that would provide the fastest cooling. Too fast and it will not dissipate the heat very well while too slow and it takes more time. The best flow rate was found to be 2 litres per minute. Luckily, tests on the element and shield life of the equipment over a 12 month period showed they were not negatively affected by the rapid cooling.
Within the first year of SINE2020 a cooling time of only 45 minutes was achieved. This is 6 x faster than the existing process. This system has been fitted to all furnaces at ISIS in a manual form for two years and over a 12 month period has saved 39 days of beam time, equivalent of up to 13 extra neutron experiments!
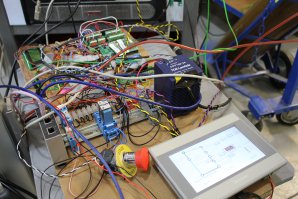
Figure 1
Of course, the development didn’t stop there. The process is simple enough but why not automate it? And, even better, make it controllable remotely?
Graham Burgess was in charge of doing the electronics for automation. He is very proud of the neat and intricate handiwork that has taken him many months. The set-up includes a user-friendly touch screen for operation and uses high quality solenoid and mass flow control valves (see Figure 1). These could extend the adaptability of the equipment for future possibilities, e.g. a user who wishes to cool their sample to a set temperature or by a set cooling rate during an experiment.
The new rapid cooling process has been well-tested and only a few small tasks remain before it is installed into the “control box” (Figure 2). Then as a fully automated system it will be tried on the ISIS instrument POLARIS to determine any tweaks that are required before the remaining manual systems are converted to automated ones.
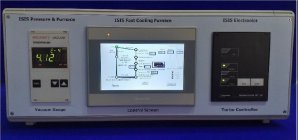
Figure 2
The remote controlled capability of this equipment will also benefit users. From the comfort of their home or hotel they can start the cooling process remotely so their sample is already at the required temperature when they arrive. This will gain them the luxury of an extra 45 minutes in bed, or perhaps a few more paragraphs of their latest paper.
Graham used the SECoP protocol for his work. This is a protocol standard introduced by the SINE2020 project that will facilitate interchangability for all sample environments so they can be used everywhere. This is also very important for companies that would consider producing this fast-cooling furnace for sale.
SINE2020 has enabled the development of this latest sample environment improvement through its funding. Now many more furnaces can be produced for instruments at ISIS and other neutron sources around the world.
In fact, through the SINE2020 collaboration, ILL are already producing them for all their instruments, although with slightly different furnace designs (resistive furnace) they are using 7cc He injections and have achieved 4 x faster cool-down times. ESS can also ensure these are added to their capabilities to enable them to collect their data quickly and efficiently from first neutrons onwards.
Acknowledgements: Chris Goodway, Paul Mcintyre, Adam Sears and Graham Burgess, ISIS
Back to The Road to the ESS
Other articles: Sample Environment, Thermally decoupling a goniometer, Improving the signal-to-background ratio, STFC